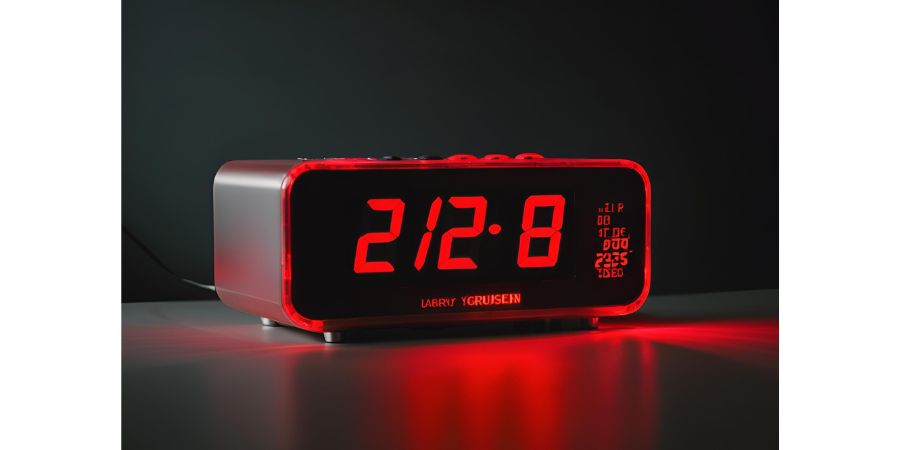
OKUMA CNC machines are known for their precision, efficiency, and reliability in the manufacturing industry. However, like any advanced machinery, they can experience errors that disrupt operations. One such issue is the OKUMA Alarm 2295 error code, which can halt production and cause significant downtime if not addressed promptly.
This error typically relates to servo drive malfunctions, encoder signal failures, or excessive load conditions affecting the spindle or axis drives. Understanding the root causes and implementing the right troubleshooting steps is essential to restoring normal machine function quickly.
In this article, we will explore the meaning of Alarm 2295, its potential causes, and step-by-step troubleshooting methods. Additionally, we’ll provide preventive maintenance strategies to help operators minimize the risk of encountering this error in the future. Whether you’re a CNC machinist, maintenance engineer, or shop owner, this guide will equip you with the knowledge needed to efficiently diagnose and resolve OKUMA Alarm 2295.
What is OKUMA Alarm 2295?
When operating an OKUMA CNC machine, encountering an Alarm 2295 error code can be frustrating, especially if it brings production to a halt. This alarm is typically related to servo drive issues, encoder signal faults, or excessive load conditions affecting the machine’s spindle or axis drives. If not addressed promptly, it can lead to unplanned downtime, costly repairs, and production delays.
1. Understanding the Alarm 2295 Error Message
The OKUMA Alarm 2295 is generally classified as a servo-related error that indicates an abnormality in the servo motor, amplifier, or feedback system. The exact wording of the alarm may vary slightly depending on the machine model and control system, but it usually points to a problem in the axis drive system or a failure in encoder feedback signals.
In simpler terms, this error occurs when the machine’s control system detects irregularities in the servo drive’s response, preventing smooth operation of the affected axis or spindle. If left unresolved, it can lead to mechanical stress, inaccuracies in machining, or even permanent damage to key components.
2. Machines and Control Systems Affected
OKUMA’s CNC machines come with a variety of OSP control systems, and the Alarm 2295 error is known to appear across multiple generations of these controllers, including:
- OSP-P Series (e.g., OSP-P200, OSP-P300) – Common in modern high-performance machining centers and lathes
- OSP-U Series (e.g., OSP-U10, OSP-U100) – Used in older OKUMA machines with servo-driven technology
- OSP-E Series (e.g., OSP-E100L, OSP-E10M) – Found in various machining centers and turning machines
Regardless of the control system, the underlying causes of Alarm 2295 are generally similar across different machine models, often pointing to servo-related issues or electrical disturbances.
3. Common Situations Where Alarm 2295 May Occur
Operators and maintenance teams might encounter the OKUMA Alarm 2295 under several different circumstances, including:
- During Machine Startup
- If the machine generates Alarm 2295 immediately after powering on, it could indicate a servo initialization failure or a problem with the encoder feedback signal.
- Loose connections, power fluctuations, or corrupted control parameters might be the cause.
- While Running High-Speed Machining Operations
- If the alarm occurs during cutting operations, it could be due to excessive spindle load, rapid acceleration/deceleration, or unstable servo tuning.
- This is especially common when working with heavy-duty materials or aggressive feed rates.
- After a Sudden Power Failure or Voltage Surge
- Electrical instability, such as power drops, surges, or unstable grounding, can cause encoder feedback errors, triggering Alarm 2295.
- If the alarm appears right after a blackout or emergency stop, it may indicate a need to check the servo system’s power supply and connections.
- Following a Machine Crash or Mechanical Overload
- If the machine has experienced a collision or an abnormal force on the spindle/axis, it might have triggered the error due to servo drive overloading.
- In this case, checking the mechanical condition of the affected components is necessary before resetting the alarm.
- After Software Updates or Parameter Changes
- If an operator recently modified CNC parameters, updated firmware, or restored factory settings, incorrect servo tuning values or corrupted encoder data might lead to Alarm 2295.
- In such cases, restoring the original parameter settings or recalibrating the servo drive system might be required.
Understanding these common scenarios and affected components will help CNC operators and maintenance teams quickly diagnose and resolve Alarm 2295, minimizing downtime and ensuring smooth machine operation. In the next sections, we will dive deeper into troubleshooting steps, effective solutions, and preventive measures to keep your OKUMA CNC machine running efficiently.
Causes of OKUMA Alarm 2295 Error Code
When an OKUMA CNC machine displays Alarm 2295, it’s signaling an issue related to the servo system, encoder feedback, electrical stability, or machine load conditions. Understanding the root cause is crucial for efficient troubleshooting and minimizing downtime.
Below, we break down the most common causes of Alarm 2295, explaining why they occur and how they affect machine performance.
1. Servo Drive Failure
The servo drive plays a critical role in controlling the motion of the machine’s axes by receiving commands from the CNC controller and converting them into precise movements. A failure in this system can trigger Alarm 2295, often due to:
- Overheating of the servo drive unit – Excessive heat buildup can degrade internal components, causing irregular motor performance.
- Worn-out or damaged servo motors – Over time, mechanical wear or improper lubrication can lead to resistance in motor movement.
- Faulty servo amplifier – If the amplifier is not delivering proper voltage or current, it can cause erratic servo responses, leading to alarm triggers.
- Loose or disconnected cables – A poor connection between the servo drive and the controller can disrupt communication, leading to a sudden error message.
🔹 Signs to look for: Unusual noises from the servo motor, fluctuating power levels, or intermittent alarm occurrences.
2. Encoder Signal Issues
Encoders are responsible for providing precise feedback about the position and speed of the machine’s axes. If the CNC system cannot accurately read encoder signals, it will trigger Alarm 2295. Common encoder-related issues include:
- Faulty or contaminated encoder – Dust, oil, or debris buildup on the encoder can interfere with signal transmission.
- Broken or misaligned encoder cables – A damaged or loosely connected encoder cable may result in signal loss.
- Interference from nearby electrical equipment – Strong electromagnetic fields from other machines can disrupt encoder signals.
- Misconfigured or corrupted encoder parameters – If encoder settings are not properly calibrated, the system may misinterpret axis positions, causing false alarms.
🔹 Signs to look for: Inconsistent axis movement, sudden stops during machining, or error messages related to feedback loss.
3. Excessive Load on the Spindle or Axis Drive
If the spindle or axis drive is overloaded, the servo system may struggle to keep up, triggering Alarm 2295. This issue often arises due to:
- Cutting parameters set too aggressively – High-speed machining with excessive feed rates or deep cuts can overburden the spindle.
- Improper tool selection – Using the wrong tool for a given material can cause excessive resistance, leading to system strain.
- Workpiece misalignment – If the workpiece is improperly clamped, the machine may encounter unexpected resistance, overloading the drive.
- Worn-out bearings or mechanical components – Friction caused by deteriorating bearings can increase motor load beyond acceptable limits.
🔹 Signs to look for: Slower-than-normal machining speeds, vibration during operation, or alarm triggers after heavy cutting sequences.
4. Electrical Interference or Wiring Faults
Electrical stability is essential for seamless CNC machine operation. Alarm 2295 can be triggered by fluctuations in power supply or poor wiring conditions, including:
- Voltage spikes or drops – Unstable power can disrupt the servo system, leading to alarm conditions.
- Loose grounding connections – Inadequate grounding can cause erratic servo behavior.
- Signal noise from nearby machinery – High-frequency electrical signals from adjacent machines may interfere with encoder or servo drive communication.
- Aging or damaged cables – Over time, cable insulation can degrade, leading to short circuits or loss of signal integrity.
🔹 Signs to look for: Alarm occurrences at random times, machine performance fluctuations after power surges, or visible wear on wiring.
5. Software or Parameter Corruption
Incorrect software settings or parameter corruption can also lead to OKUMA Alarm 2295. Common causes include:
- Recent software updates or control system resets – If new firmware is not properly configured, the system may misinterpret servo feedback.
- Incorrect servo tuning settings – Improper gain adjustments can cause instability in the servo system.
- Loss of stored machine parameters – If CNC parameters were accidentally reset or corrupted, the machine may not function as expected.
- Unexpected system shutdowns – Power failures during operation can lead to data corruption, affecting servo communication.
🔹 Signs to look for: Alarm occurrences after software updates, changes in servo tuning settings, or loss of previously saved configurations.
Troubleshooting OKUMA Alarm 2295
When an OKUMA CNC machine displays Alarm 2295, it’s essential to approach troubleshooting systematically. Since this alarm is typically related to servo drive malfunctions, encoder feedback issues, electrical problems, or excessive load conditions, diagnosing the exact cause is crucial to resolving the error and preventing further downtime.
Below is a step-by-step troubleshooting guide to help you identify and fix the issue efficiently.
Step 1: Check System Diagnostics on the OSP Control Panel
OKUMA CNC machines provide built-in diagnostic tools on their OSP control panel, which can offer valuable insights into the nature of the error.
✅ How to check diagnostics:
- Navigate to the Alarm History screen to view details about Alarm 2295.
- Check for any related alarm codes that might indicate encoder, servo, or amplifier issues.
- Access the Servo Monitor function to check servo load, position feedback, and any anomalies in axis movement.
🔹 What to look for:
- If the diagnostics show servo overload, focus on mechanical load and drive settings.
- If feedback errors are detected, check encoder connections and signals.
- If the system logs power-related issues, inspect electrical wiring and grounding.
Step 2: Inspect Servo Drives and Amplifiers
A malfunctioning servo drive or amplifier is one of the most common causes of Alarm 2295. These components control the movement of the machine’s axes and must function correctly.
✅ How to inspect the servo system:
- Listen for abnormal sounds from the servo motors—grinding or whining noises can indicate internal damage.
- Check the servo amplifier’s LED indicators—flashing error codes can help pinpoint issues.
- Measure servo drive voltage and current levels using a multimeter to ensure they are within specifications.
- Swap the servo drive unit with a known working one (if available) to see if the error clears.
🔹 What to look for:
- Overheating, burn marks, or unusual noises indicate a failing servo drive.
- Inconsistent voltage readings suggest electrical instability or amplifier failure.
Step 3: Verify Encoder Feedback and Connection
Encoders provide critical position feedback to the CNC controller. If their signals are interrupted, inaccurate, or lost, Alarm 2295 can occur.
✅ How to check encoders:
- Inspect the encoder cables for signs of wear, cuts, or loose connections.
- Use a multimeter to test encoder voltage output and ensure proper signal flow.
- If available, use a diagnostic software tool to check real-time encoder data.
- Replace the encoder with a known working unit if troubleshooting suggests a failure.
🔹 What to look for:
- If the machine registers no movement or erratic movement, the encoder is likely faulty.
- If the problem persists after replacing the encoder, check related wiring or parameter settings.
Step 4: Examine Wiring and Power Supply Stability
Electrical fluctuations, poor grounding, or damaged wiring can interfere with the servo system and trigger Alarm 2295.
✅ How to check wiring and power supply:
- Ensure the machine’s power supply voltage is stable and within the manufacturer’s recommended range.
- Inspect all servo motor and encoder wiring for loose terminals or frayed cables.
- Check the grounding connections—poor grounding can lead to electrical noise interfering with signals.
- Use an oscilloscope or power quality analyzer to detect transient voltage spikes or fluctuations.
🔹 What to look for:
- Sudden alarm occurrences may indicate power instability or faulty wiring.
- Frequent alarms during specific operations might suggest electrical interference from nearby equipment.
Step 5: Check Spindle or Axis for Mechanical Overload
If the spindle or axis drive is overloaded, the servo system may struggle to maintain precise movement, leading to Alarm 2295.
✅ How to inspect for overload conditions:
- Check if the machine load meter is consistently running at high levels.
- Verify that the cutting parameters (feed rate, depth of cut, and tool selection) are within recommended limits.
- Manually move the affected axis using the handwheel or jog function—if movement feels rough or sluggish, there could be excessive mechanical resistance.
- Inspect bearings, ball screws, and lubrication systems to ensure smooth operation.
🔹 What to look for:
- If the alarm appears only during heavy machining, consider reducing the feed rate or checking for worn-out mechanical components.
- If movement is restricted, clean and lubricate axis components.
Step 6: Reset Alarms and Test System Operation
Once potential issues have been identified and addressed, reset the alarm and test the machine to confirm that the problem has been resolved.
✅ How to reset Alarm 2295:
- Turn off the CNC machine and wait for a few minutes before restarting.
- Navigate to the Alarm Reset function on the control panel.
- If the alarm persists, recheck servo parameters and perform a system reboot.
- If necessary, perform a factory reset of the control system (only as a last resort, and ensure all parameters are backed up).
🔹 What to look for:
- If the alarm does not return, monitor the machine for a few hours to ensure stability.
- If the alarm reoccurs, repeat diagnostics to pinpoint any remaining issues.
Recommended Tools and Diagnostic Software
To effectively troubleshoot Alarm 2295, having the right tools can make a significant difference:
- Multimeter – For checking voltage and continuity in servo and encoder circuits.
- Oscilloscope – To analyze electrical signals and detect fluctuations.
- OKUMA Diagnostic Software – Available for OSP controllers to monitor servo performance.
- Handheld Encoder Tester – Useful for verifying encoder output signals.
- Thermal Camera – Helps detect overheating components in the servo drive system.
Common Fixes for OKUMA Alarm 2295
Encountering OKUMA Alarm 2295 can be frustrating, especially when it disrupts production. Fortunately, many cases can be resolved with basic troubleshooting steps before calling for technical support. The solutions below cover quick fixes and when to consider component replacements or software adjustments to restore machine functionality.
1. Restarting the Machine and Resetting Errors
One of the simplest yet effective first steps in resolving Alarm 2295 is to perform a system restart and error reset. This helps clear temporary faults caused by power fluctuations, software glitches, or transient servo errors.
✅ How to restart and reset errors:
- Turn off the CNC machine completely and wait for at least 5–10 minutes.
- Restart the machine and navigate to the Alarm History screen to review error details.
- Use the RESET or CANCEL button on the OSP control panel to clear active alarms.
- If the alarm persists, try rebooting again while ensuring all servo systems are initialized properly.
🔹 When this works:
- If the alarm was triggered by a minor software glitch or a temporary servo feedback issue.
- If the machine experienced a power interruption or an emergency stop condition.
🔹 When to move on to deeper troubleshooting:
- If the alarm immediately returns upon restarting.
- If additional error codes appear alongside Alarm 2295, indicating hardware issues.
2. Checking Servo and Encoder Connections
Loose, damaged, or disconnected wiring between the servo drive, amplifier, and encoder can cause Alarm 2295 by preventing proper communication between components.
✅ How to check and secure connections:
- Inspect all wiring connected to the servo drive, encoder, and power supply.
- Look for loose connectors, frayed cables, or bent pins in plugs.
- Use a multimeter to check continuity in encoder signal cables.
- Ensure that all servo drive connections are securely fastened and free from dust or corrosion.
- If possible, swap the encoder cable with a spare to rule out cable damage.
🔹 When this works:
- If the error was caused by a disconnected encoder cable or a weak electrical connection.
- If the issue occurs intermittently, which might indicate vibration-induced cable wear.
🔹 When to move on to deeper troubleshooting:
- If the encoder connections are intact but the alarm persists, the encoder itself may be faulty.
- If multiple alarms appear related to power or feedback loss, the issue might be within the servo amplifier or control board.
3. Adjusting Servo Gain and Tuning Parameters
If the servo system is not properly tuned, it can lead to erratic movements, excessive load on the motor, or improper encoder feedback—potentially triggering Alarm 2295. Adjusting servo gain and tuning parameters can help stabilize performance.
✅ How to adjust servo gain and tuning:
- Access the Servo Adjustment menu in the OSP control panel.
- Use the Automatic Servo Tuning function if available to let the machine optimize settings.
- If tuning manually, start with lower gain values and gradually increase while monitoring performance.
- Run a test cycle with reduced feed rates and acceleration settings to see if the alarm reoccurs.
🔹 When this works:
- If the alarm was triggered by incorrect servo tuning settings or excessive vibration in high-speed operations.
- If the machine exhibits jerky movements, overshooting, or instability in axis motion.
🔹 When to move on to deeper troubleshooting:
- If tuning does not improve performance or if the alarm appears even with conservative settings.
- If you suspect hardware issues such as a worn-out servo motor or drive amplifier failure.
4. When to Replace Faulty Components (Encoders, Servo Amplifiers, Motors)
If basic troubleshooting does not resolve Alarm 2295, it may indicate that a critical component has failed and requires replacement.
✅ Signs that replacement may be necessary:
- Encoder Failure:
- Machine cannot properly detect axis positions.
- Encoder readings fluctuate or show inconsistencies.
- Replacing the encoder cable does not fix the issue.
- Servo Amplifier Failure:
- Alarm occurs even after checking wiring and connections.
- The servo amplifier overheats or shows flashing fault indicators.
- Voltage readings are outside normal operating ranges.
- Servo Motor Failure:
- Motor struggles to maintain position or produces abnormal noises.
- Machine experiences sudden stops, stalls, or irregular movements.
- Load meter consistently shows excessive readings, even with no cutting load.
🔹 When to attempt repairs instead of replacement:
- If components show intermittent failure, try reseating connectors or cleaning electrical contacts.
- If the issue appears after a power surge, check fuses and power supply components before replacing major parts.
5. Updating or Restoring Control System Software and Parameters
If Alarm 2295 appears after a software update, system crash, or parameter reset, restoring factory settings or updating firmware may help.
✅ How to restore or update system settings:
- Navigate to the Control System Backup & Restore Menu on the OSP interface.
- If you recently changed parameters, revert them to previous known working values.
- If available, update to the latest OKUMA firmware provided by the manufacturer.
- If necessary, reload machine-specific servo and spindle tuning parameters from backup files.
- Perform a soft reset after changes to ensure the system applies updates correctly.
🔹 When this works:
- If the alarm started after modifying machine parameters or updating software.
- If system logs indicate corrupted firmware or missing configuration data.
🔹 When to move on to hardware checks:
- If restoring software does not fix the problem, hardware failure is likely involved.
- If alarms persist even after resetting to factory settings, further diagnostics are required.
Preventing Future Occurrences of Alarm 2295
While troubleshooting OKUMA Alarm 2295 is essential for restoring machine operation, preventing it from happening again can save time, reduce downtime, and extend the life of CNC components. A proactive maintenance strategy ensures that servo drives, encoders, and electrical systems remain in optimal condition, minimizing the chances of unexpected errors. Below are key preventive measures to keep your OKUMA CNC machine running smoothly.
1. Regularly Inspecting Servo and Drive Systems
Since Alarm 2295 is often related to servo drive or motor failures, routine inspections can help identify early warning signs before they lead to a breakdown.
✅ Preventive maintenance tips:
- Schedule monthly checks on all servo drives and amplifiers for abnormal heat buildup or vibrations.
- Inspect for loose connections, damaged cables, or worn-out servo motors.
- Use a multimeter to check voltage stability in the servo drive circuit.
- Monitor servo load meters—a gradual increase in load percentage can indicate impending failure.
- Keep servo cooling fans and heat sinks clean to prevent overheating issues.
🔹 Why this helps:
Regular inspections catch minor wear and tear before it escalates into major servo drive failures that trigger Alarm 2295.
2. Keeping Encoders and Feedback Systems Clean
Encoders play a crucial role in providing position feedback, and any contamination or signal disruption can cause the machine to misinterpret axis movement.
✅ How to maintain encoders and feedback systems:
- Clean encoders regularly using non-abrasive cloths to remove dust, oil, and debris.
- Ensure encoder cables are properly shielded to prevent electrical noise interference.
- Avoid exposing encoders to coolant splashes or excessive vibration, which can affect accuracy.
- Test encoder signal strength periodically to detect signal degradation before failure occurs.
🔹 Why this helps:
A well-maintained encoder system ensures accurate positioning and prevents feedback errors that can trigger Alarm 2295.
3. Monitoring CNC Parameters and Error Logs
Many servo and spindle-related errors can be prevented by tracking system logs and adjusting CNC parameters before they lead to an alarm condition.
✅ Best practices for monitoring CNC parameters:
- Regularly review alarm history on the OSP control panel to identify recurring issues.
- Analyze servo performance data, including gain values, speed, and load trends.
- Monitor CNC machine usage patterns—sudden parameter changes can indicate an issue.
- Adjust servo tuning parameters gradually when optimizing machine performance to avoid instability.
🔹 Why this helps:
By keeping an eye on error logs and adjusting CNC settings proactively, you can detect trends that lead to recurring alarms and fix issues early.
4. Using Recommended Voltage Stabilizers and Surge Protectors
Fluctuations in electrical power supply can cause servo drive faults, encoder signal loss, or amplifier failures, all of which can trigger Alarm 2295.
✅ How to stabilize power supply:
- Install voltage stabilizers to maintain consistent power levels to the CNC machine.
- Use surge protectors to prevent damage from sudden electrical spikes.
- Ensure proper grounding and eliminate electrical noise sources from surrounding equipment.
- Check power cables and distribution boards for signs of wear or loose connections.
🔹 Why this helps:
Protecting your machine from electrical instability ensures that servo and encoder systems function without interference, reducing the risk of Alarm 2295.
5. Implementing Predictive Maintenance with IoT
Advancements in Industry 4.0 and IoT (Internet of Things) technology allow for real-time monitoring of CNC machine health, making it easier to predict and prevent failures before they happen.
✅ How predictive maintenance helps:
- Install IoT sensors on servo motors, encoders, and amplifiers to track real-time performance.
- Use AI-driven analytics to detect anomalies in servo load, speed, or temperature trends.
- Set up automated maintenance alerts when key parameters deviate from normal ranges.
- Perform data-driven servicing rather than relying on fixed maintenance schedules.
🔹 Why this helps:
Predictive maintenance helps identify issues before they trigger alarms, reducing unscheduled downtime and improving machine efficiency.
Conclusion
OKUMA Alarm 2295 is a critical issue that can disrupt CNC machining operations, leading to costly downtime and potential damage to machine components. By understanding its causes—ranging from servo drive malfunctions and encoder signal failures to electrical disturbances and mechanical overloads—operators and maintenance teams can take a systematic approach to troubleshooting. Identifying whether the alarm occurs during startup, high-speed machining, or after a power fluctuation can provide valuable clues to pinpoint the root cause.
Resolving this alarm requires a combination of diagnostic steps, including checking connections, verifying power stability, and recalibrating servo parameters. Additionally, implementing preventive maintenance, such as regular inspections and software updates, can significantly reduce the chances of encountering this issue in the future.
By staying proactive and well-informed, CNC machinists, maintenance engineers, and shop owners can keep their OKUMA machines running efficiently, ensuring smooth production and maximizing operational uptime.